
粒子機零件今日要聞信息
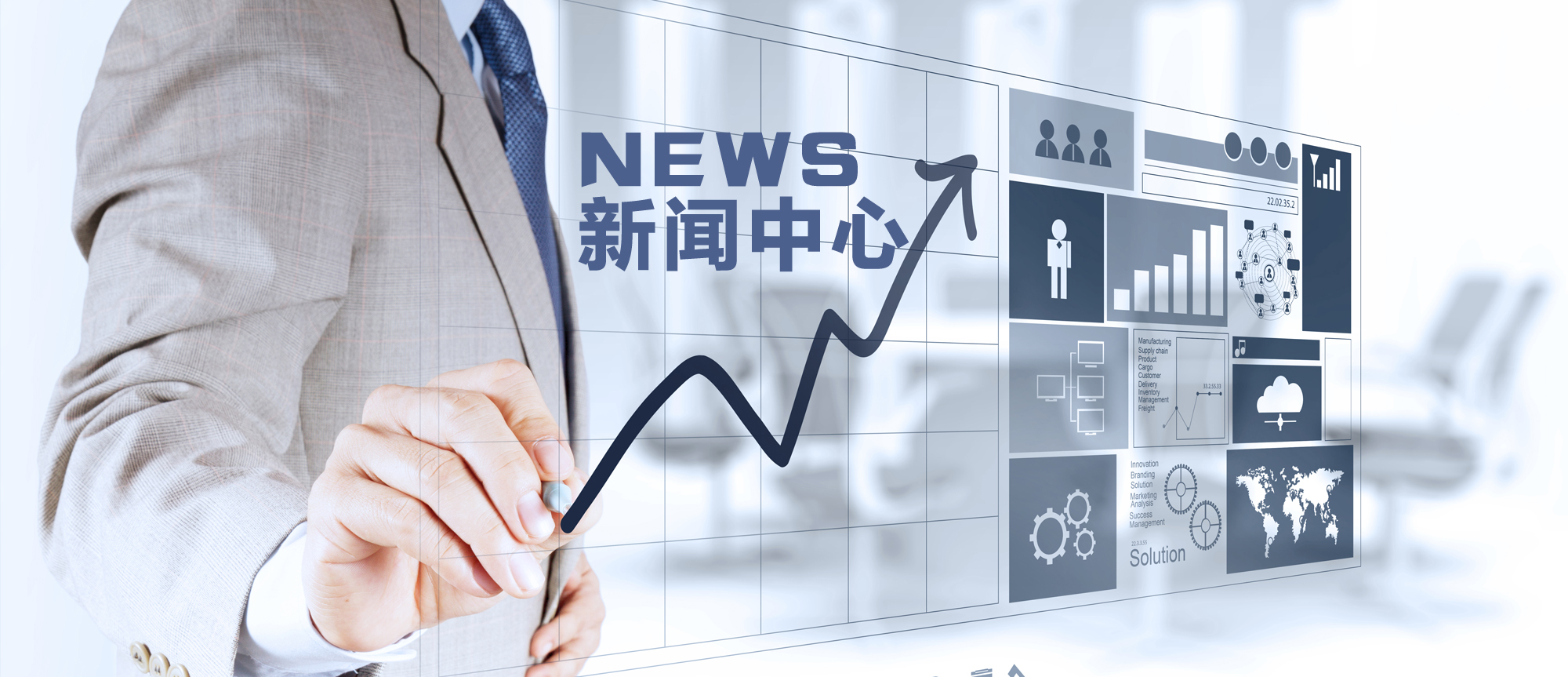
富通新能源 > 動態 > 顆粒機配件新聞動態 > > 詳細
襯板用中鉻各種馬氏體不銹鋼的科研
披露時:2014-07-03 08:26 來源于:不同
濕式球磨機襯板長期處于堿性或酸性液體介質中工作,同時受到磨球、礦石的沖擊、磨損和介質的腐蝕。失效形式主要是磨損、腐蝕和斷裂。為保證襯板的使用壽命,襯板材質應具備合理的力學性能匹配,即具有高強度、高韌性和高硬度,同時還應具有一定的抗腐蝕能力。目前,國內常用的球磨機襯板材料是ZCMn13,使用后其殘體表面硬度只有HB260一350,沖擊硬化特性未能充分發揮,耐磨性較差,壽命較短。同時,高錳鋼塑變抗力較低,襯板在使用過程中往往容易變形,造成襯板之間相互咬合,使維修拆卸困難。為解決高錳鋼襯板在使用中存在問題,提高襯板使用壽命,近年來我們研制開發了低合金鋼襯板,經工廠生產試用,效果良好。但是,由于低合金鋼主要組織是馬氏體和少量碳化物,耐磨性尚有待提高,而且,球磨機襯板極易在使用后期出現斷裂失效現象,使用壽命仍得不到顯著的提高,富通新能源銷售球磨機、雷蒙磨粉機等磨機機械設備。
根據以上存在的問題,我們進行了襯板用中鉻合金耐磨鋼的研制。該試驗通過適當提高C、Cr含量,優選合金元素的加入量,增加鋼組織中碳化物量,獲得點球狀或短桿狀碳化物形態。同時,為提高鋼的沖擊韌性,試驗中經過熱處理工藝的選擇,使鋼獲得馬氏體+下貝氏體+殘余奧氏體+碳化物組織,從而使該鋼材具有優良的綜合機械性能,提高了耐磨性和使用壽命。
1、試驗鋼化學成分的選擇
本試驗以MnSiCrMo系鋼為基礎,采用少量、多元綜合合金化的成分設計方法,通過加入碳化物形成元素Cr、Mo、Mn、B和非碳化物形成元素Si,發揮多元合金元素的綜合作用,使鋼能在空氣中淬硬,獲得馬氏體+貝氏體+碳化物組織,有效地提高鋼的淬透性,在保證鋼的主要化學成分合適的基礎上,再添加微量元素進行微合金化,不顯著增加成本卻可以明顯地細化晶粒,提高沖擊韌性和耐磨性。
根據合金元素的作用和襯扳的使用條件,以及在多次成分篩選試驗的基礎上,確定試驗鋼的化學成分如表1。
2、試驗內容和研究方法
試驗鋼按成分設計配料后,采用15 kg中頻感應電爐熔煉,熔煉溫度達1550℃,經最終脫氧后出爐,澆注溫度為145℃。試樣采用頂注法澆注成11mm×11mm×55mm和∮14mm×160mm試樣,然后磨削成10mmx 10mm×55mm無缺口沖擊試樣和∮13mmX160mm抗彎強度試樣。顯微組織試樣和硬度試樣,均從沖擊試樣或抗彎強度試樣上截取。在擺錘式沖擊試驗機、材料強度試驗機和洛氏硬度計上分別進行沖擊韌性、抗彎強度和硬度實驗。采用日立S-570掃描電鏡觀察分析金相組織。
2.1奧氏體化溫度試驗
為掌握奧氏體化溫度對試驗鋼的晶粒度、硬度、沖擊韌性、抗彎強度等的影響,進行奧氏體化溫度選擇試驗,以確定試驗鋼合適的奧氏體化溫度。試驗工藝如圖1所示。將沖擊韌性和抗彎強度試樣各分為4組,每組5個試樣,試驗后進行機械性能試驗。經過比較不同奧氏體化溫度對機械性能的影響后(詳見本文3試驗結果與分析),確定試驗鋼合適的奧氏體化溫度為1020℃。
2.2降溫淬火和回火溫度試驗
根據奧氏體化溫度試驗確定的奧氏體化溫度1020℃,先進行降溫淬火處理,然后進行回火溫度試驗。降溫淬火工藝如圖2所示。淬火加熱先升溫至1020℃,保溫30mim,以促進奧氏體均勻化,使合金碳化物溶解于基體內,提高試驗鋼的淬透性;為防止試驗鋼晶粒粗大,避免淬火應力過大,產生淬火裂紋,再將試樣隨爐冷至920qC保溫30 mim。在此過程中溶解于基體中的碳化物以點球狀或短桿狀析出,提高了試驗鋼的硬度和沖擊韌性。隨后出爐風冷。回火工藝如圖3所示,將經過降溫淬火后的沖擊韌性和抗彎強度試樣各分為5組,每組5個試樣,回火后進行機械性能試驗。經比較不同回火溫度對機械性能的影響后,確定試驗鋼合適的回火溫度。
2.3利用鑄造余熱等溫淬火試驗
該試驗直接利用鑄造余熱,將澆注后冷卻至奧氏體結晶完成溫度的試樣,從鑄型中取出快冷至下貝氏體轉變溫度區進行保溫,進行下貝氏體轉變,使試驗鋼獲得下貝體組織,從而提高試驗鋼的沖擊韌性、節約能源,降低生產成本,縮短生產周期,提高生產率。
首先澆注試樣,當試樣在鑄型內結晶凝固并冷卻至奧氏體結晶完成溫度時開箱,將試樣在空氣中快速冷至略高于等溫淬火溫度后,放入導熱率低、隔熱性能好的介質中保溫緩冷一段時間,使試驗鋼獲得下貝氏體組織,再將試樣從保溫介質中取出冷至室溫。因此,試驗主要進行保溫介質、開箱溫度和保溫溫度的選擇。
等溫淬火過程,必須滿足鑄件打箱后高溫快冷和低溫慢冷的要求。高溫快冷主要是避免試驗鋼產生珠光體型組織,這可以在開箱后空冷或風冷實現;低溫慢冷的目的,是使試驗鋼在下貝氏體轉變區有足夠的時間進行下貝氏體轉變,以形成下貝氏體組織。因此,必須選擇導熱系數小、保溫性能好的保溫介質,才能在連續冷卻時模擬等溫淬火過程完成下貝氏體轉變。根據要求,我們選擇了硅酸鋁耐火纖維材料,這種材料能在927—1343℃范圍內直接與熱源接觸長期使用,導熱率低,隔熱性能好,具有很好的抗熱震性(溫度急變)和抗機械震動性。
開箱溫度選擇為850℃,9000℃,950℃,1020℃。通過試驗最終選擇950℃進行開箱,在此溫度開箱得到的組織比較細小,試樣的綜合機械性能較好。
保溫溫度選擇試驗工藝如圖4所示。將試樣分為6組,每組5個試樣,每組在規定的保溫溫度下放進保溫介質中,保溫30 min后取出空冷至室溫,進行機械性能試驗。
在試驗中,開箱溫度和保溫溫度的測量采用經過標定校驗的熱電偶插入鑄型內進行。在生產中為了便于操作,預先測量某一鑄件(襯板)自澆注后冷卻至開箱溫度和保溫溫度的時間,在利用鑄造余熱等溫淬火過程中,只要根據冷卻時間即可判斷出鑄件的開箱溫度和保溫溫度,從而進行開箱冷卻和等溫淬火。
3、試驗結果與分析
3.1奧氏體化加熱溫度對晶粒度的影響
用淬硬法測定試驗鋼在不同奧氏體化溫度下的晶粒度見表2。
結果表明,試驗鋼的奧氏體晶粒隨溫度升高而長大的傾向很小,加熱至970~1020℃時,晶粒度仍很小,可見試驗鋼中加入的微合金化元素Ti、V、RE細化晶粒作用明顯。
3.2奧氏體化溫度對試驗鋼性能的影響
奧氏體化溫度對試驗鋼機械性能的影響如圖5示。試驗鋼的硬度隨著奧氏體化溫度的升高逐漸增高,到了920℃硬度值增加緩慢,并保持在HRC62附近。沖擊韌性隨奧氏體化溫度的升高先降后升,950℃是轉折點,溫度升至1020℃時,沖擊韌性達到最大值。抗彎強度隨奧氏體化溫度的變化類似于沖擊韌性。當奧氏體化溫度(850℃)較低時,試驗鋼組織中存在較多的鐵素體,合金碳化物以團塊狀分布在晶界,因而試驗鋼的硬度較低,沖擊韌性和抗彎強度較高。隨著奧氏體化溫度的升高,試驗鋼中鐵索體逐漸消失,馬氏體隨之增多,硬度逐漸升高,沖擊韌性逐漸降低。當溫度升高至950℃以上,分布在晶界中的合金碳化物逐漸溶解于晶粒內,促使奧氏體成分均勻化,多元合金元素的綜合作用得以發揮,提高了試驗鋼的淬透性,因而,沖擊韌性和抗彎強度逐漸升高,硬度保持在較高的值。當輿氏體化溫度達到102℃,試驗鋼的綜合機械性能較好。
3.3回火溫度對試驗鋼性能的影響
回火溫度對試驗鋼機械性能的影響如圖6示。試驗鋼的硬度沒有隨回火溫度的升高而降低,回火溫度達480℃時,硬度仍保持在HRC58左右,可見試驗鋼具有良好的抗回火穩定性。沖擊韌性在330℃回火時達到最大值,隨后逐漸下降,但低于430℃回火沒有出現明顯的回火脆性。可見試驗鋼的回火脆性比較小。當回火溫度低于430℃時,抗彎強度在1650—1800MPa波動,高于430℃回火時,抗彎強度逐漸升高。由圖6見,經1020℃降溫淬火,再經330℃回火的試驗鋼具有良好的綜合機械性能。相應的金相組織見圖7。由圖可見試驗鋼的組織為馬氏體+貝氏體+殘余奧氏體+碳化物。
3.4利用鑄造余熱等溫淬火的保溫溫度對機械性能的影響
利用鑄造余熱等溫淬火的保溫溫度對機械性能的影響如圖8所示。在較低溫度保溫時,沖擊韌性隨保溫溫度的升高而增加,保溫溫度為330℃時達到最大值。試驗鋼的硬度比較高,保持在HRC59~63之間,保溫溫度對硬度值的影響不大。抗彎強度有隨保溫溫度升高而降低的趨勢。當開箱溫度為950℃,保溫溫度為280℃~330℃時,試驗鋼具有較高的綜合機械性能,但比按1020℃降溫淬火加330℃回火處理的試驗鋼的機械性能稍低。相應的金相組織見圖9。由圖可見試驗鋼的組織為馬氏體+貝氏體+殘余奧氏體+碳化物。
由于利用鑄造余熱等溫淬火處理的試驗鋼沒有經過再加熱處理,而是直接開箱空冷至保溫溫度,放進保溫介質中保溫。因而,試驗鋼晶界間存在斷網狀或塊狀碳化物,使沖擊韌性、抗彎強度下降,而硬度較高。實際上,試驗鋼在保溫介質中并不是等溫,而是緩慢冷卻,若冷卻速度大了,在貝氏體轉變區獲得貝氏體的量就少,這樣,試驗鋼的沖擊韌性得不到顯著的提高。
4、結論
(1)由于多元舍金元素的綜合作用,試驗鋼具有晶粒細小、淬透性好、綜合機械性能良好的特點。
(2)經1020C降溫淬火,再經330C回火的試驗鋼的組織為馬氏體+貝氏體+殘余奧氏體+碳化物,試驗鋼的機械性能:HRC= 58~60、沖擊韌性a=20. 30 J/cm2、抗彎強度a,,=1600—1800 MPa。
(3)利用鑄造余熱進行等溫淬火熱處理不但可以使試驗鋼獲得馬氏體+貝氏體+殘余奧氐體+碳化物組織,而且可以節約能源,縮短生產周期,降低生產成本,提高生產率。當開箱溫度為9500C,保溫溫度在280—330℃時,試驗鋼的機械性能:HRC= 59—63、沖擊韌性a=15~24 J,cm2、抗彎強度a:850~920 MPa,比按1020℃降溫淬火加330℃回火處理的試驗鋼的機械性能稍低。
(4)中鉻合金耐磨鋼可用作球磨機襯板材料。生產中根據襯頓使用的工況和材質要求的不同以及工廠的實際生產條件,可選用利用鑄造余熱等溫淬火工藝或降溫淬火+回火工藝進行熱處理。