
桔桿粉碎性機報道的動態
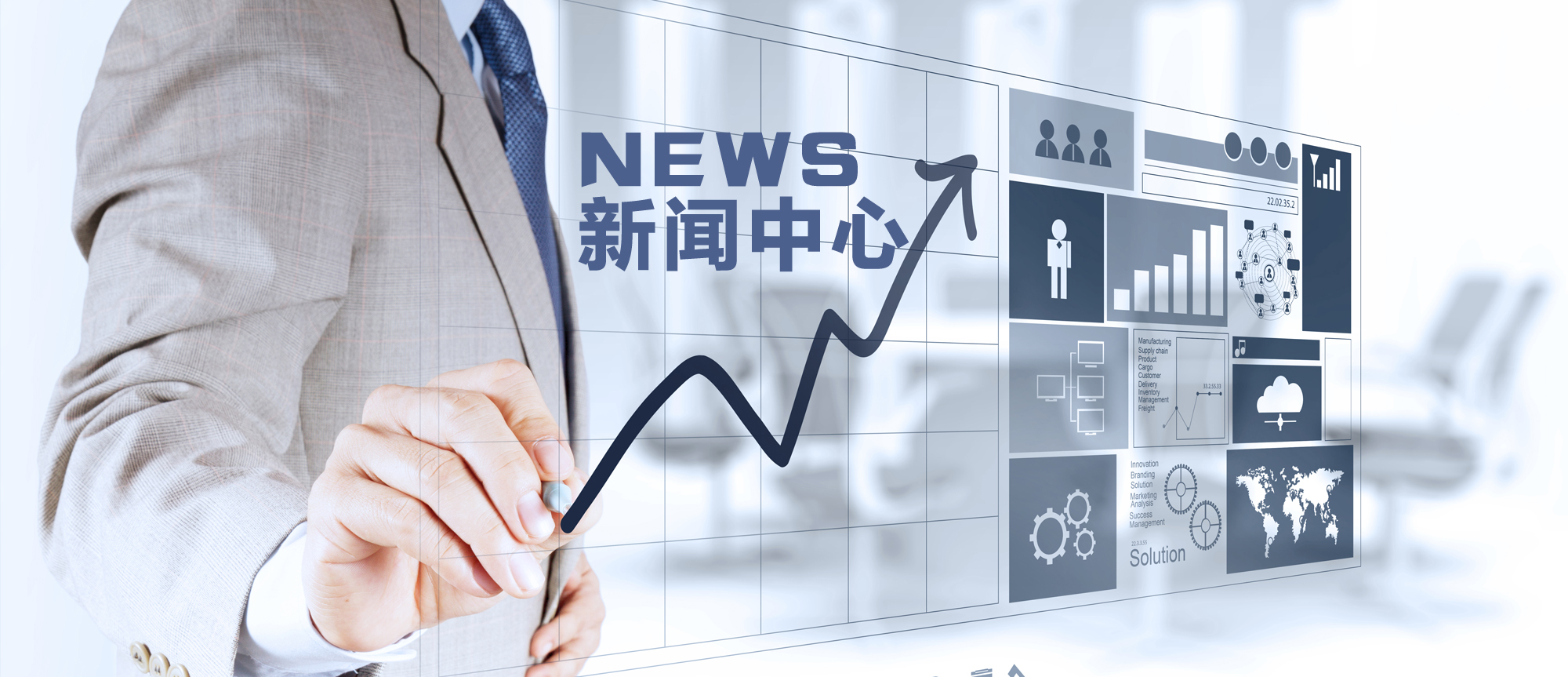
富通新能源 > 動態 > 秸稈粉碎機新聞動態 > > 詳細
PCZ強效擊碎機在混凝土行業中的軟件
發表時長:2014-06-14 07:57 由來:不明
0、引言
近年來投產的新型干法水泥線中,生料系統普遍應用下列三種工藝布置方式:①單段錘破+立磨;②單段錘破+高效細碎機+管磨;③單段錘破+擠壓磨+管磨。但在已有的許多老線中,生料系統仍采用傳統單段錘破+管磨工藝布置方式,其入磨粒度僅能控制在≤25mm(篩余15%)范圍內。而此粒度顯然無法滿足降低磨機系統綜合電耗的目的。受場地和空間限制,老線較難改造成新型破碎工藝系統。在工況條件不變前提下,要進一步提高現有磨機系統產量并降低電耗,較佳途徑是降低入磨粒度。因此有必要研制一種出料粒度≤15mm(篩余5%~10%)的新型單段錘破。我院在多年來研制推廣PCX型高效細碎機經驗和技術的基礎上,研制了PCZ強力破碎機。
1、破碎機理
PCZ強力破碎機基本結構見圖l,其破碎是基于單顆粒破碎和顆粒體的群體料層破碎相結合的破碎方式。進機的大塊礦石首先由錘盤支托,受高速旋轉的錘頭打擊,礦石被一塊一塊地敲脫下來。進機的較小礦石,則直接飛向反擊板破碎并反彈,與后續飛來的礦石再次空中碰撞。此粗碎階段屬單顆粒破碎。反復擊打變小的礦石,在破碎腔里繼續被打擊破碎,在壓力作用下,料層厚度被逐級壓縮.快速通過破碎板與轉子之間的顎口進入下機體,在轉子圓周與篦板之間狹小空間形成的“沸騰床”里,被擠壓、剪切、搓磨,合格粒度的礦石由篦縫排出機外。此細碎階段屬顆粒體的群體料層破碎。
2、技術特點
2.1破碎腔型優化
反擊破碎腔的結構特點決定了設備的能力、功耗、磨耗及產品粒度等重要指標。為了充分發揮單顆粒破碎和顆粒體的群體料層破碎的功能,通過在計算機上進行動態模擬試驗,分析了破碎腔內破碎板與轉子圓周之間幾何曲線形狀及顎口間隙大小對物料的通過量以及破碎效果的影響,找出了兩者之間較佳破碎嵌入曲線和嵌入角,并優化設計了反擊破碎腔。使整個破碎腔的顆粒群密度保持了一個由疏變密的較佳速率以及破碎腔齒角的較佳動態性能。其破碎腔型優化前后結構見圖2(圖中R710是轉子回轉半徑)。
2.2轉子結構優化
為使轉子具有將大塊礦石瞬間擊碎并迅速達到所需粒度的能力,同時保證大塊礦石進機時電動機電流基本不發生大的波動,優化了轉子結構:①盡量增加錘頭外伸量;②根據錘頭磨損及轉子動平衡情況,建立錘頭排列配置模型;③將錘盤、端盤等焊接成一體,增強轉子結構強度;④根據礦石特性和含土及水分不同,對轉子做針對性的設計。
2.3錘頭材質合理選用
根據石灰石中游離Si02含量、物理性能、泥沙和水分含量等,選用超高錳合金或合金鋼模鍛錘頭。
對高硬度物料選用超高錳合金錘頭(ZCMn17Cr2MoVTi)。該材質的錘頭由于加入Cr、Mo和V等元素使晶粒細化,提高了錘頭的強度和韌性。通過采用合理的熱處理工藝,錘頭的金相組織以奧氏體為主,加少量的碳化物和馬氏體。這種錘頭在高硬度物料的劇烈沖擊下會迅速產生奧氏體的冷作硬化效果,可由原始硬度HB200左右提高到HB460-500。圖3為PC21414強力破碎機在破碎20萬噸石灰石后超高錳合金錘頭的磨損情況。
對中硬或偏軟的物料則選用合金鋼模鍛錘頭。這種錘頭不僅整體抗拉強度達850MPa,而且有相當的塑性和韌性。在錘孔加工后對錘端打擊區進行淬火,其表面硬度可達HB410-460。
2.4排料篦子優化
優化排料篦子的主要目的是提高破碎效率及對原料的適應性。通過研究篦條的截面形狀及走向、刃口角度、篦縫大小及變化、排列方式,找出了較佳的顆粒體的群體料層破碎密度及密度變化率。另外,老式篦子的調節只能使中部達到與轉子有合理的間隙,而前后兩段均擴張增大,從而極易形成墊層,不僅使篦子的通過能力減小,產量降低,而且墊層又加速錘頭的磨損并縮短壽命。優化后篦子采用可收縮結構,可以消除墊層現象的產生,使破碎機在錘頭磨短之后仍保持正常的工作狀態。
2.5安全保護裝置
除本體內設計了排鐵門安全機構、在強力作用下可后退的反擊破碎板、能3600轉動的鉸接錘頭速三項進鐵保護功能外,在自動控制上考慮了下列兩個安全保護措施:
1)應用模糊數學控制原理,破碎機主電動機裝有功率變送器,根據其檢測到負荷信號可自動調節喂料設備的速度,使破碎機始終在較佳負荷和較合理電耗狀態下運行。在超負荷等異常情況下控制系統自動發出報警信號或給出停車控制動作。
2)控制系統將根據軸承溫度檢測裝置傳輸的信號,設定上限報警值,異常時發出報警信號或給出停車控制動作。
2.6加工和裝配工藝改進
2.6.1 錘盤和端盤表面堆焊
錘盤及端盤外緣部分要求有較高的耐磨性,同時錘軸孔的部位還需較高的韌性。為此,先在錘軸孔外周用D212焊條堆焊2.5 mm厚緩沖層,然后整個輪緣再用TM-55焊條堆焊8mm厚的耐磨層。錘盤及端盤母材采用低碳厚鋼板,焊接性較好,但由于板材及堆焊層較厚,焊接時熱影響區有可能產生熱裂紋。為避免此現象,采用火焰對錘盤及端盤進行預熱,堆焊時保持該溫度。圖4為采用上述堆焊工藝的錘盤使用6個月后的情況,從圖中可見,幾乎未磨損。
2.6.2 主軸承裝配
由于高載荷和工作條件苛刻,PCZ強力破碎機的轉子選用了大游隙的圓錐調心滾子軸承,它的自調心功能可補償兩軸承座的不同心及可能產生的轉子偏斜。主軸承裝配水平直接影響到軸承溫度及使用壽命。我們通過測量由于內圈的受力膨脹而減少的徑向游隙來決定圓錐調心滾子軸承的配合。
例:將22344CAKJW33/C3軸承(PC21414強力破碎機選用)裝配到主軸錐套上,用塞尺測到起始游隙為0.286mm。從表l查得,當起始游隙減少0.102~0.140mm時為適宜的配合,所以鎖緊螺母必須擰至徑向游隙達到0.146—0.184mm范圍內,取0.166mm。
3、應用
上海浦東水泥廠原為700t/d熟料生產線,2003年燒成系統技改后達到了1100/d規模,但石灰石破碎系統未作同步改造,嚴重制約了生料磨能力,并影響到窯的產量。2004年2月該廠委托我院對石灰石破碎系統進行技術改造。
3.1 技改工程簡介
改造前有兩條相同的∮l130mmx1150mm雙轉子錘式破碎機(允許人料粒度≤350mm,臺產約30t/h,出料粒度≤20mm)破碎石灰石生產線,受板喂機及破碎設備制約,要求外購石灰石粒度≤350mm,物料由駁船運到碼頭后卸人地坑,經800mm中型板喂機(允許物料粒度$350mm,輸送量l5—110m3/h)分別喂入兩臺破碎機。
存在的問題:
1)該破碎機屬老式雙轉子錘破,由于設有盛料筐、轉子上錘頭排列稀疏和轉速慢(錘頭線速度僅為19.3m/s)等原因,存在產量低、排料中粗顆粒多、來料中泥沙含量較多時排料篦子易堵塞等缺陷。由于破碎機與生料磨產量不匹配,實際生產中放寬了篦縫,出料粒度放寬至20—40mm,單機產量約50t/h,但仍無法滿足生料磨實際生產需求。
2)因礦山資源緊張,外購石灰石粒度已無法滿足≤350mm要求。
3)來料中泥沙含量高達10%—30%,水分高達5%~10%,經常造成破碎機篦子堵塞,電動機過載跳閘。
另外,為了不影響全廠正常生產,整個改造工程要求在7d內完成。
針對上述情況,確定改造一條石灰石破碎線,生產能力達到90~130t/h,最大進料粒度達到600mm。另一條線保持原狀不變,作為備用和補充。
具體技改措施如下:
新換一臺PC21414強力破碎機,最大進料粒度增大到600mm左右,出料粒度≤15mm(篩余5010~10%)。板喂機輸送量達130t/h左右,角度從22。抬高到23°,并相應縮短長度。并根據該廠石灰石原料中泥沙和水分含量大特點,對轉子及篦子結構作了針對性設計。該機工藝簡圖見圖5。
破碎機基礎利用原機地腳螺栓固定,兩者之間設一個鋼結構過渡架。因原破碎機基礎承載力不夠,利用原基礎下方出料皮帶廊空間,設計了一個八字型鋼結構支架加固原基礎承載梁,其下部支腿與預埋鋼板焊接固定,上部長方形鋼梁用膨脹螺栓與承載梁底部固定。新做一個較大鋼結構支架作為電動機基礎,其內圈利用原電動機基礎地腳螺栓進行固定,外圈周邊用地腳螺栓穿過樓板固定。其加固簡圖見圖6。由于準備工作充分,整個工程僅用5d時間就順利結束。
3.2調試
從2004年5月31日至6月3日,共負荷投料25h,主機運行平穩,用HY-103型測振儀測出主軸承座最大振動烈度為4mm/s.最大振幅為0.12mm。均符合IS02372的振動評定標準和JC/T922-2003《水泥工業用破碎機技術條件》行業標準。主軸承溫度穩定在40~60℃,小軸承溫度30-40。C,空載電流30~50A,負載電流160~200A。進料平均粒度約200mm,最大粒度500mm,平均產量約100t/h。
針對調試中暴露的問題,進行了及時處理:
1)電動機傳動裝置小軸承座水平方向振動偏大,超過了IS02372中≤11.2mm/s評定標準。用千分表檢查發現聯軸器同軸度安裝誤差過大,為此經重新調整,將其最大誤差控制在0.2mm以內,解決了水平振動過大問題。調整前后小軸承座振動烈度見表2。
2)檢測主軸承溫度的顯示儀不工作。經檢查發現WZPM-201型端面熱電阻上分度號與溫度顯示儀上分度號不匹配。我們更換了分度號為Pt100的XMT智能溫度數顯儀,并將上限報警溫度設定為75℃。
3)頂襯板螺栓易松動。我們將螺栓由M20增大到M27,強度等級由4.8級提高到8.8級,機腔和襯板上螺孔用手提式旋磨機現場擴孔,最后上緊頂襯板并用雙螺母鎖緊。
4)大帶輪一側密封環發熱。設計圖上密封環內徑與主軸公差為∮180H7/h6,實際加工件間隙為上限,加之破碎機運行后振動使大帶輪與密封環端面未壓緊,造成密封環與主軸間有相對轉動而發熱。為此在密封環上增加了4個緊定螺釘,避免了相對轉動。
5)板喂機頭罩嚴重變形。頭罩系原破碎機頭罩改裝而成,鋼板太薄強度不夠。為此,用lOmm鋼板重做了一個頭罩,里面鑲16Mn襯板。對前墻及頂部作了進一步加固。
6)出料皮帶上間隔3—4m有40 ~60mm大塊漏料。經實地觀察,漏料系破碎機內反彈石塊從鏈板與接料溜子底邊之間空隙中彈射出來,并經料斗直接落入出料皮帶上造成的。其原因是板喂機頭輪伸人頭罩接料溜子的深度不夠,鏈板與接料溜子底邊之間空隙過大,膠皮不起作用。改進措施是將接料溜子接點移到頭輪中垂線之下,并盡量減少與鏈板間空隙,接料溜子底部安裝一塊伸入鏈板凹槽內厚橡皮擋板,使機內反彈石塊重新進入機腔內破碎。
3.3使用效果
PC21414強力破碎機自2004年6月初投運以來,已成為該廠1100t/d生產線提供原料的主導設備,到2005年9月,累計破碎石灰石40多萬噸。
1)原料適應性
由于該廠外購右灰石受制于供應商,進廠原料中摻雜了大量濕泥沙,當泥沙含量高達10%—30%,水分5%~10%時,一般能正常運轉。在上海6、7月梅雨季
節,曾發生過被堵的事件。后來通過降低板喂機轉速,
減少破碎量以及對泥沙含量超過30%、水分超過
10%的原料先晾曬后破碎,使問題得到了解決。
2)安全性
在調試階段曾發生過頂襯板螺栓松動脫落,頂襯板落人下機腔情況。在運行2個月后因振動停機檢查時發現斷了一個錘頭,錘軸上只剩錘柄,而錘頭已從排鐵門中穿過進入料庫。檢查篦子、錘盤及反擊板等均無損傷,說明它的安全性是比較好的。
3)運轉的平穩性
主軸承座用HY-103型測振儀測定空載和負載時振動烈度為:水平0.10—0.34cm/s,軸向0.10 ~0.4cm/s,垂直0.12~0.16cm/s,表明它的運轉是平穩的。而且工作電流穩定在160~200A范圍內,沒有大起大落的現象,表明設計的主參數和慣量恰當。
4)生產能力
根據用戶要求,本機按90—130 t/h設計,并留有20%的余量。實際使用表明,上述指標已經達到。目前喂料量控制在100—130 t/h范圍內。通常在黃梅雨季喂料量適當減少。據統計全年平均產量約lOOt/h。
5)出料粒度
經取樣篩分后出機粒級分布如下:0~3mm占35%,3~5mm占25%,5~lOmm占20%,10~15mm占16%,≥15mm占4%。比預期指標要好。
6)電耗
本機由一臺160kW電動機拖動,其負載電流波動范圍160~200A,實際運行功率約在74—92kW范圍,平均電耗小于0.92kWh/t。
7)易損件的磨耗
第一套錘頭使用6個月后更換,共破碎石灰石約18萬噸,新錘頭總重1 564.65kg,換下錘頭總重1283.0lkg,凈消耗量281.64kg,錘頭金屬磨耗為1.56g/t,錘頭消耗成本約為0.13元/t。更換錘頭時檢查篦板、反擊板、破碎板、錘盤及端盤等均未發現明顯磨損,錘軸抽取檢查基本無磨損。
8)不足之處
由于板喂機改造受資金限制,沒有達到預期效果,最大進料粒度限制在500mm以下,破碎機能力沒有充分發揮出來。另外,破碎含泥沙和水分高的石灰石時其電耗和錘頭磨耗尚不十分理想,錘頭消耗成本也偏高。
4、結束語
從上述測試數據和實際使用效果來看,PCZ強力破碎機基本上達到了原定各項技術經濟指標。通過一年多連續帶負荷運行,表明該機設計參數較合理,制造加工質量較好,為老線石灰石破碎技術改造提供了一種比較可靠的破碎設備。今后的研制方向是進一步降低出機粒度,并向大型化發展。